Grinding skill that determines the identity of an optical element
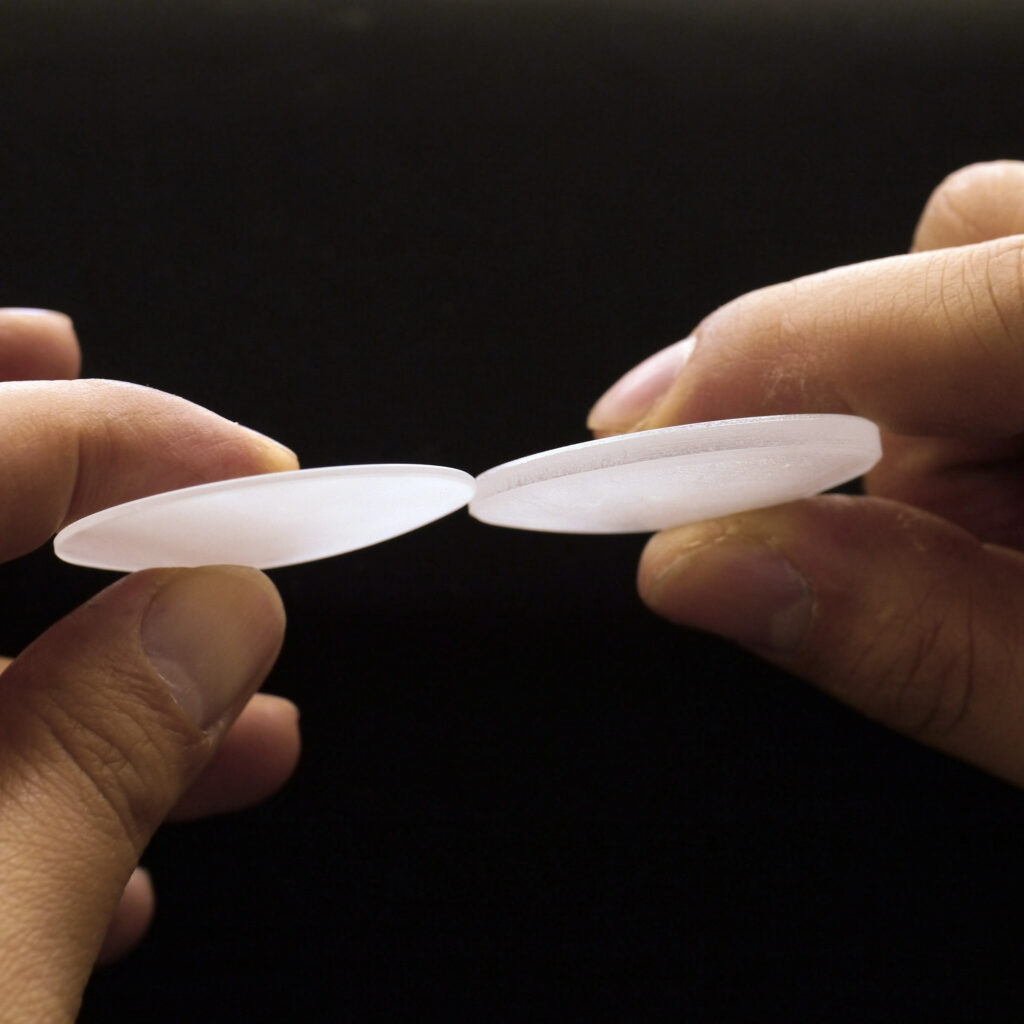
An interchangeable lens has several optical elements inside the barrel. They are all widely different from one another in terms of size, concavity vs. convexity, and optical characteristics such as refractive index. One of the key processes for making these optical elements is grinding. The above photograph compares a glass disc (right) that has been roughly shaped by pressing and an optical element (left) that has been ground to the surface curvature specified in the design specifications. They noticeably differ in thickness. In grinding, the minute material inconsistencies near the surface are removed and only the good quality material at the core is kept for the element. This process of grinding the material to a higher level of purity is exactly the same concept of grinding rice down to the “starchy kernel” that is used to brew premium “sake”.

Grinding is done on a machine known as a “curve generator.” It presses a curved diamond wheel diagonally against the optical glass disc. Optical elements can be manufactured to practically any curvature by changing the angle at which the wheel contacts the disc. Both convex and concave optical elements are shaped one at a time to the curvature that yields the specified refractive index. The ground surfaces look a cloudy white like frosted glass, but this process determines the precision of the element’s curvature for the most part or, in other words, grinding determines the identity of the optical element.
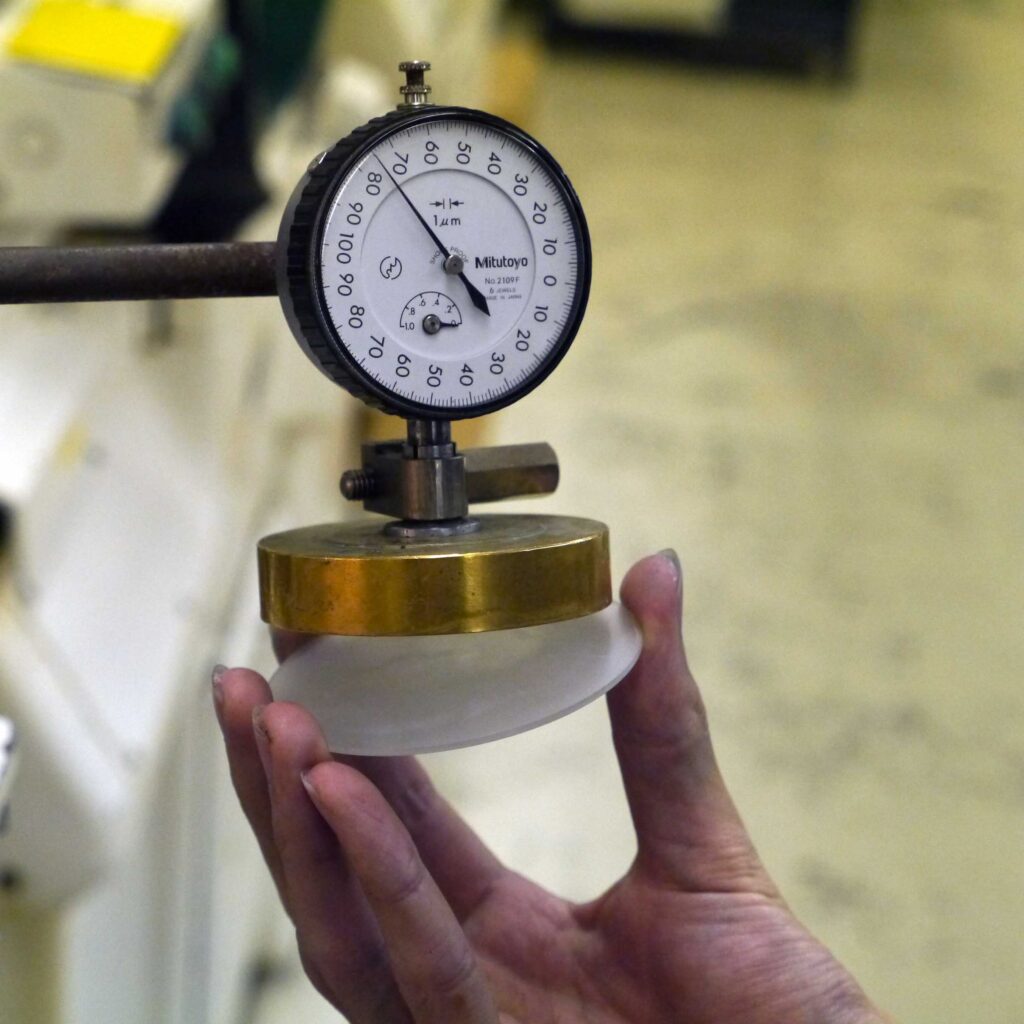
Optical element’s curvature is measured with a dial indicator called spherometer that detects the height difference between contour of the disc and its center. It determines how far the curvature deviates from a standard value when the probe that extends from the center of the gauge is aligned with the center of the disc. However, this indicator is not set to a design value. Instead, it is deliberately set to a slightly smaller value in order to prevent over-correction in the following polishing process. You do not want to over-polish the disc when finishing the optical element. The key point of the subsequent process is to polish the element with the minimum necessary load. This “sense of moderation” is a prized skill at Cosina that only comes with experience and technology.