“Ink coating” that accentuates the eye line
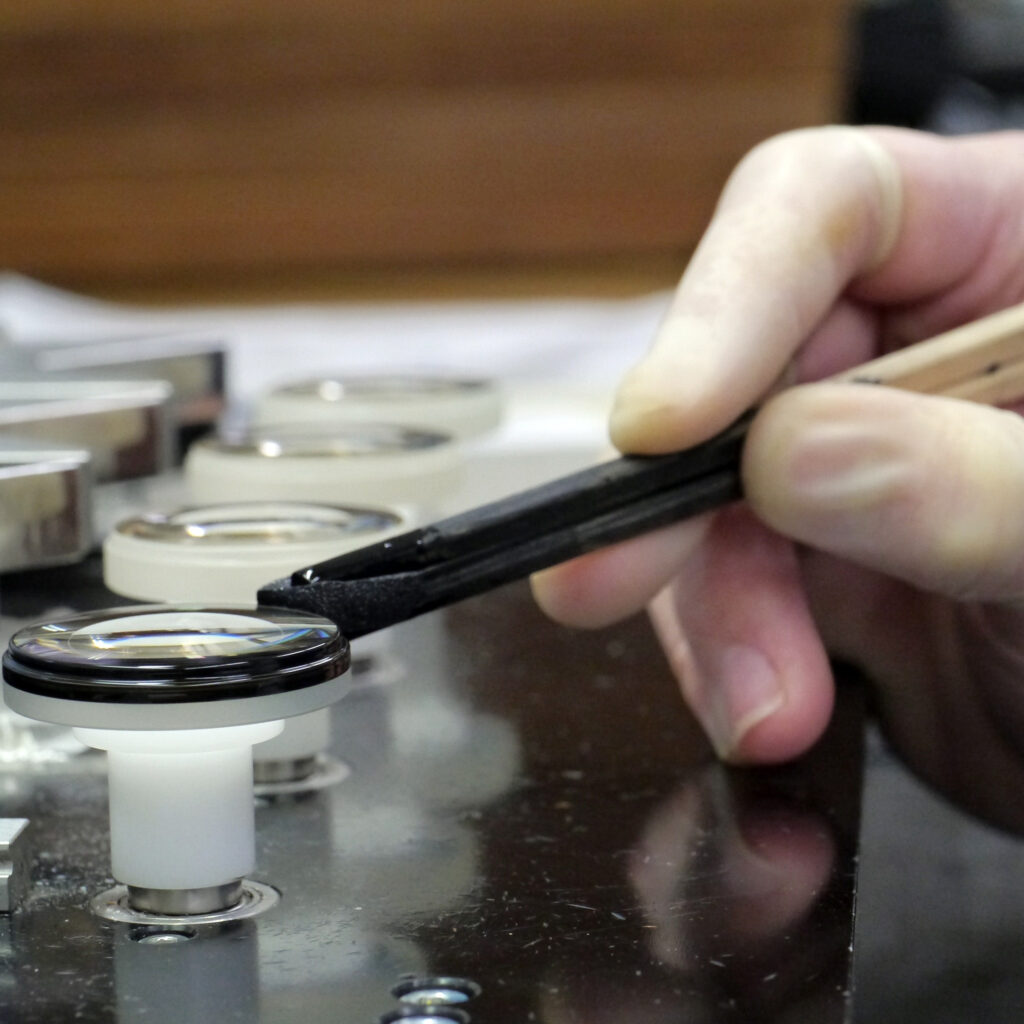
An element is quietly rotating on a motor-driven lathe after being locked in place by negative pressure. The washed end face after centering and edging looks like a piece of frosted glass. The process of applying an antireflection coating is called “ink coating.” Like balsam in 043 (Gluing elements by assessing center), the word “ink” is still used today though Japanese ink was originally used in the pioneer days. Applying ink to the element evenly and smoothly requires skillful handiwork that is difficult to mechanize. The coating is being applied by gently pressing a tip of a paint stick against the end face of the rotating element. This is how precision optical components are made, yet an air of intense concentration quietly permeates in the workplace as if you were watching a traditional artisan at work.
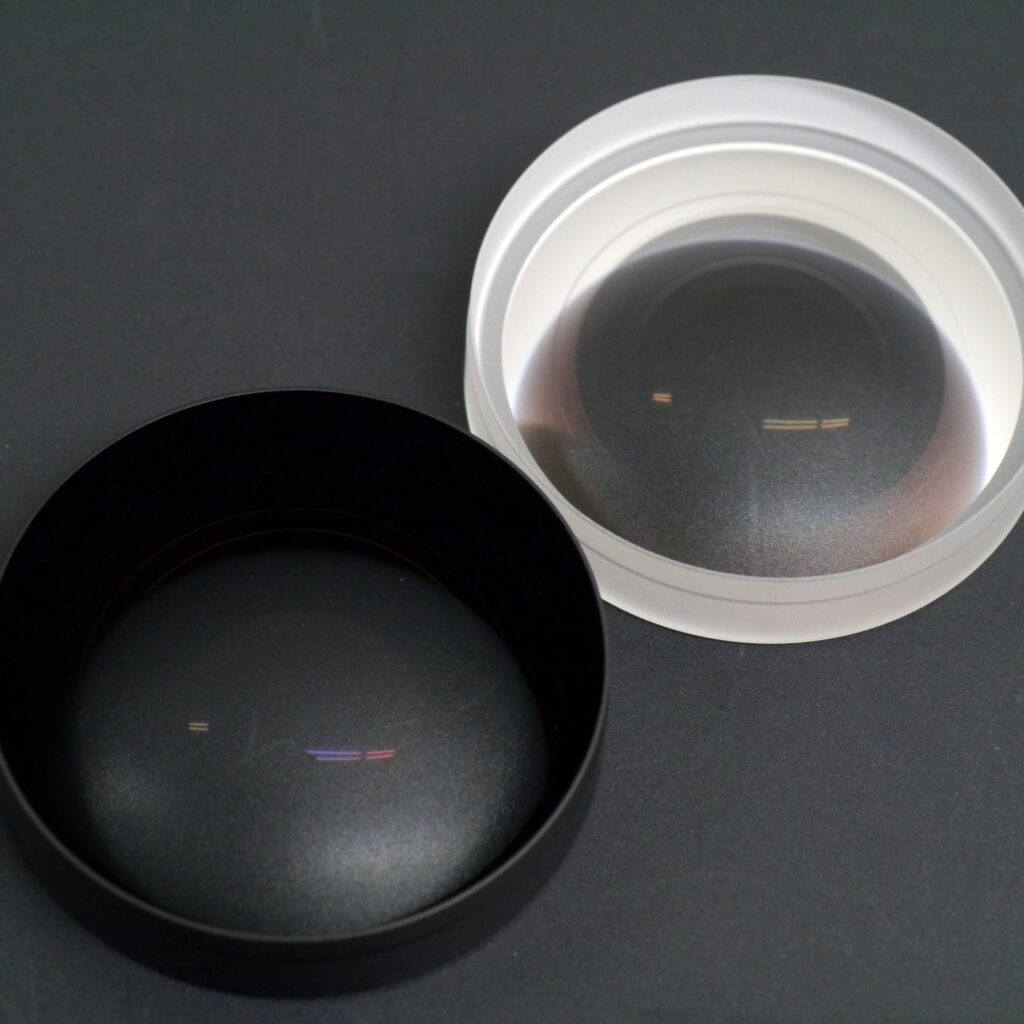
Depending on whether it is coated with ink or not, optical characteristics of even the same lens greatly change. In particular, for devices that require the entry of light such as photography lenses, this ink edge-coating is effective towards preventing the reflection of diagonal rays of light that enter the edge of the lens from outside the range of the targeted image and resultantly degrade image quality. In addition to such a practical effect, the perfectly ink-coated lens appears more beautiful than one that has just a ground texture and white end face. The ink coating gives the lens a mysterious look as if you were peering down an old well. In a certain way, it acts like makeup that gives a strong accent to eyes.
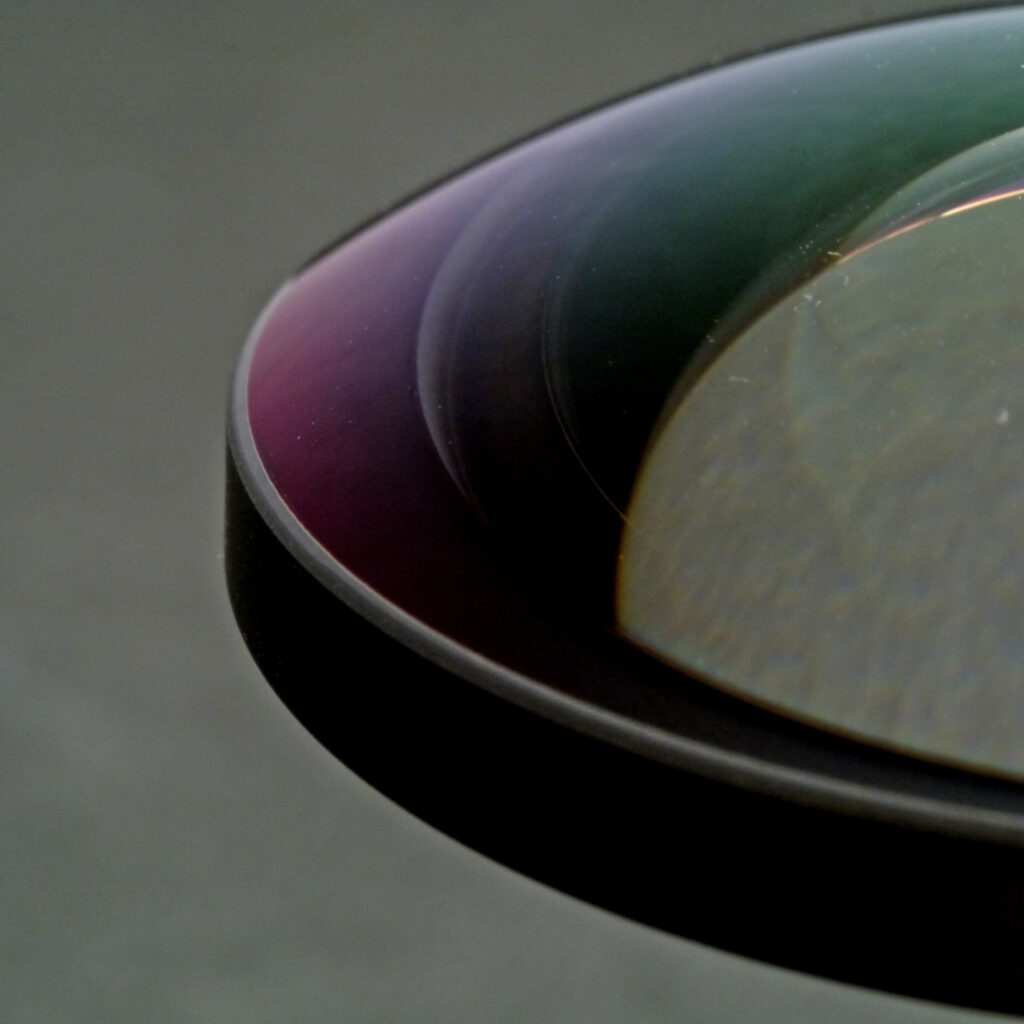
In the ink coating for interchangeable lenses for photography, the coating is applied not only to the edge of the element but also to the part of its surface about 0.2 mm inside from the edge. This contributes to making the appearance of the lens better by emphasizing the eye line. But, rather than the purpose of enhancing aesthetic effects, it is mainly intended to improve optical performance. The application of a small amount of antireflection coating to the element surface gives the effect of diaphragm. And, it plays a role of cutting a diagonal ray of light that have adverse effects on image quality.