Instruments and skills used in vacuum deposition
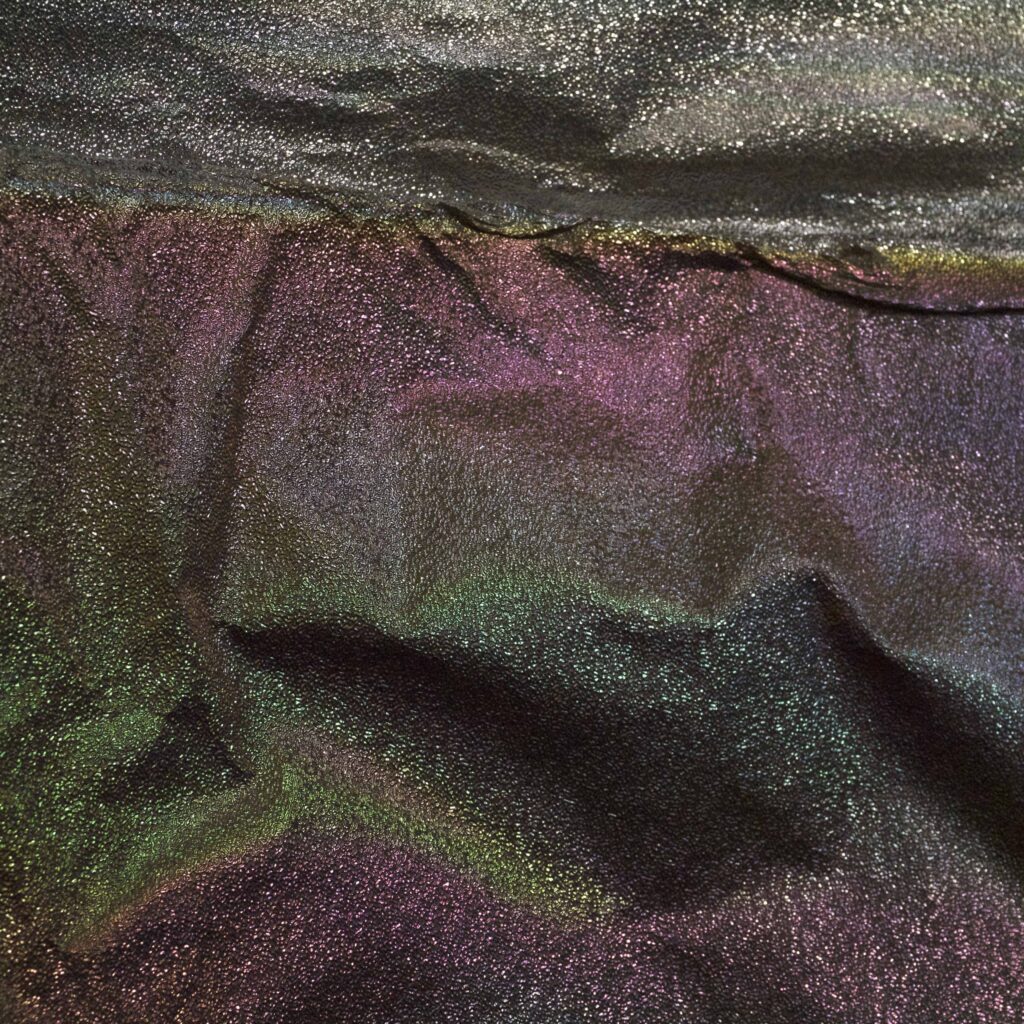
The above pattern looks like a work of abstract art that depicts the colors of a rainbow, of a microscopic view of a mineral. Actually, the above photograph is a close-up of the aluminum foil attached to the inside wall of the vacuum deposition system used for applying antireflection coatings to optical glass. In a vacuum created by removing the air in an enclosed chamber, gas molecules can move about over longer distances without colliding with each other. Coatings are applied to optical glass based on that principle. A coating material that has been vaporized in a vacuum can move freely about the chamber and form thin films. Like the surface of a high-end optical lens, this rainbow pattern appears on the inner wall as it becomes coated with various materials.
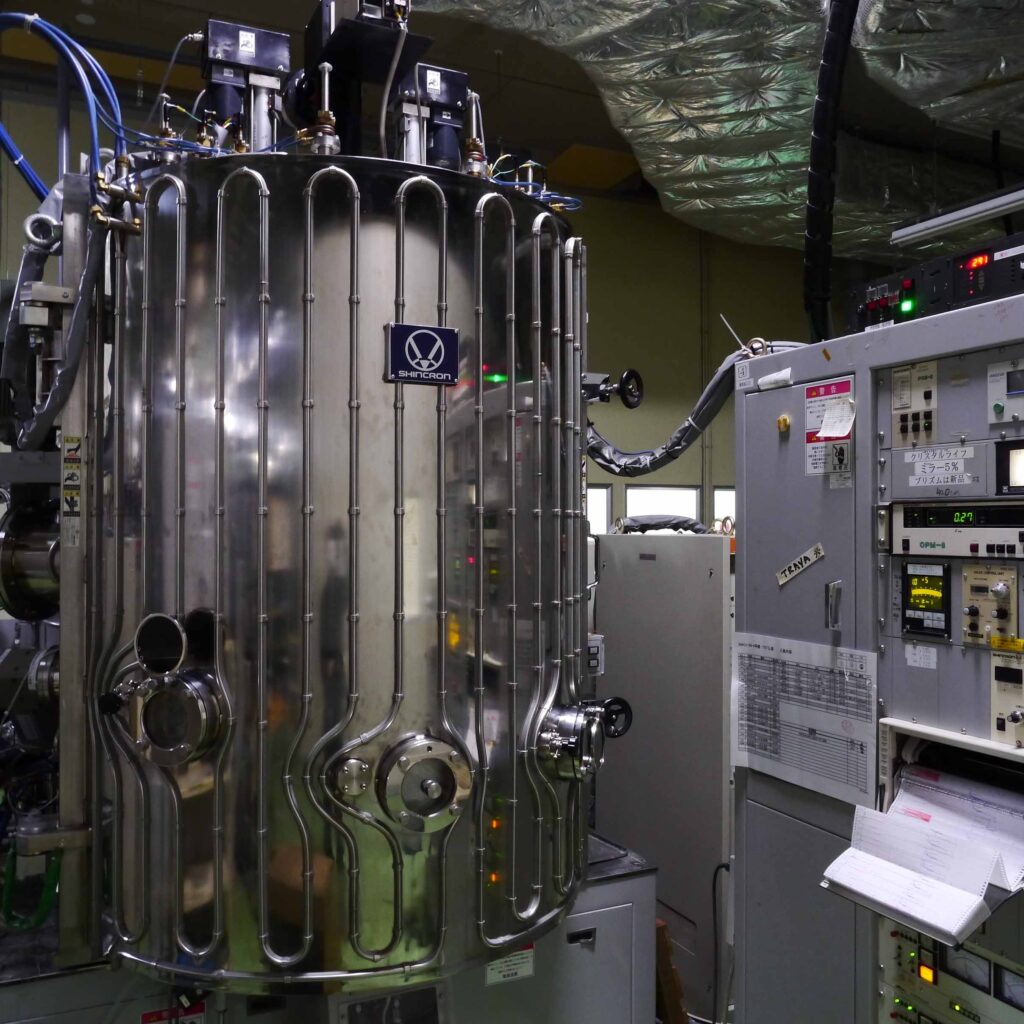
To form thin films on the surface of optical glass, a vacuum is required. Vacuum pumps, valves, and pipes for removing the air are attached to a stainless steel chamber. Also, the chamber is equipped with a drive mechanism required for the coating process, as well as various types of sensors. Even if the air is removed by the vacuum pump, a small amount of gas remains in the chamber. So, it is particularly important to know the internal state of the chamber. In addition to a vacuum gauge for measuring the degree of vacuum, potentiometers that measure residual gases by type and pressure are used to monitor the trace amounts of water, nitrogen, and oxygen. The combined use of these sensors makes it possible to reproduce the desired conditions to a high degree. We also measure the difference between systems and use tools customized for each system.

This electron beam heating device is used to vaporize and adhere coating material to the surface of optical glass at a lower temperature than the deposition temperature, and then to solidify the material as a thin film. In this process, the vacuum, temperature, diameter and incidence of the electron beam emitted during vapor deposition as it moves in an arc under magnetic force, and coating material conditions are monitored in order to thoroughly eliminate any factors that prevent the desired environment from being compromised. And, each coating layer is sampled and film thickness is controlled on the nano-order.