Satin texturing by sandblasting
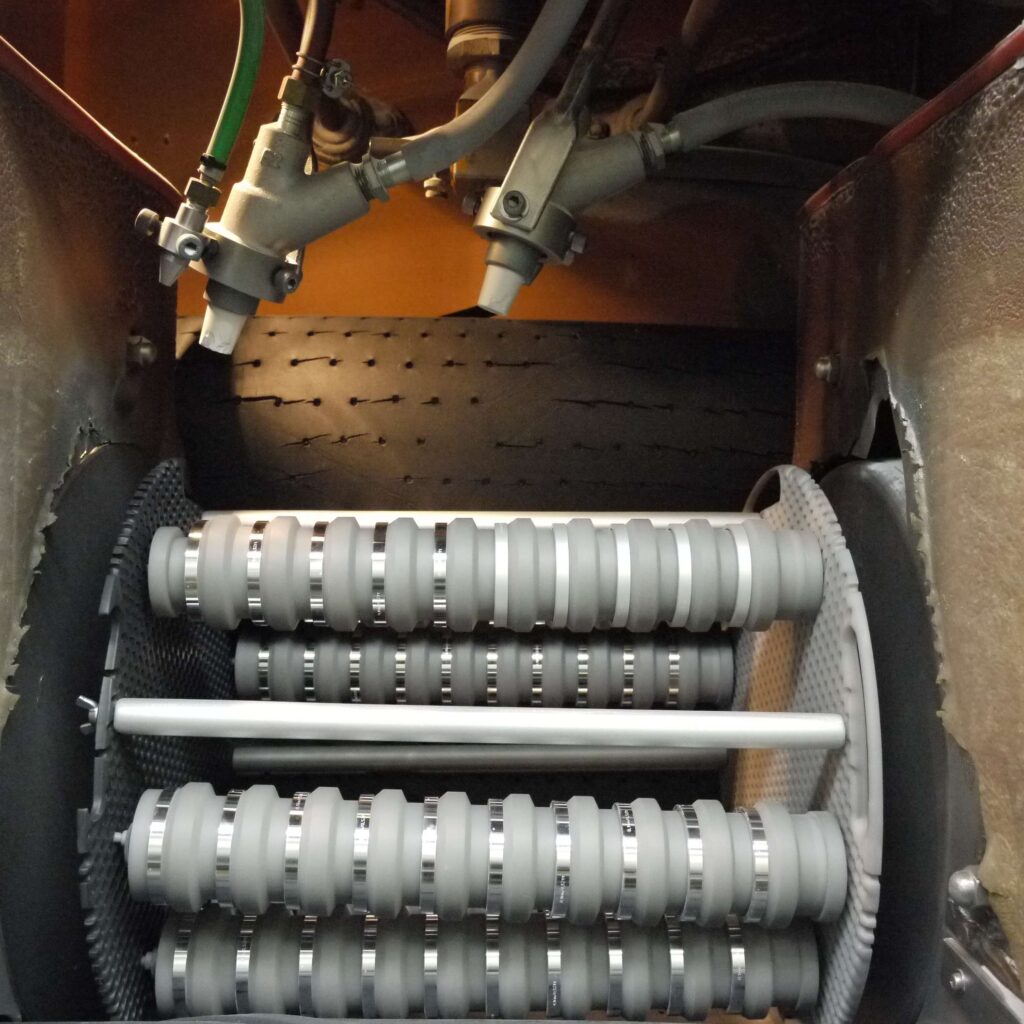
Machined metal surfaces are smooth and shiny like a mirror. But, as such, they are easily scratched and feel cold and sticky when touched. So, dulling the surfaces slightly gives them a satin finish and texture. The process for doing this is known as “sandblasting.” It is used on most of the bare metal surfaces that users handle on the high-end optical products that Cosina makes. Sandblasting sprays a tiny granular abrasive over the metal surface using a blaster gun and compressed air. Simple ring-shaped parts are set in an automated machine as shown in the above photo and finished all at the same time in batch.
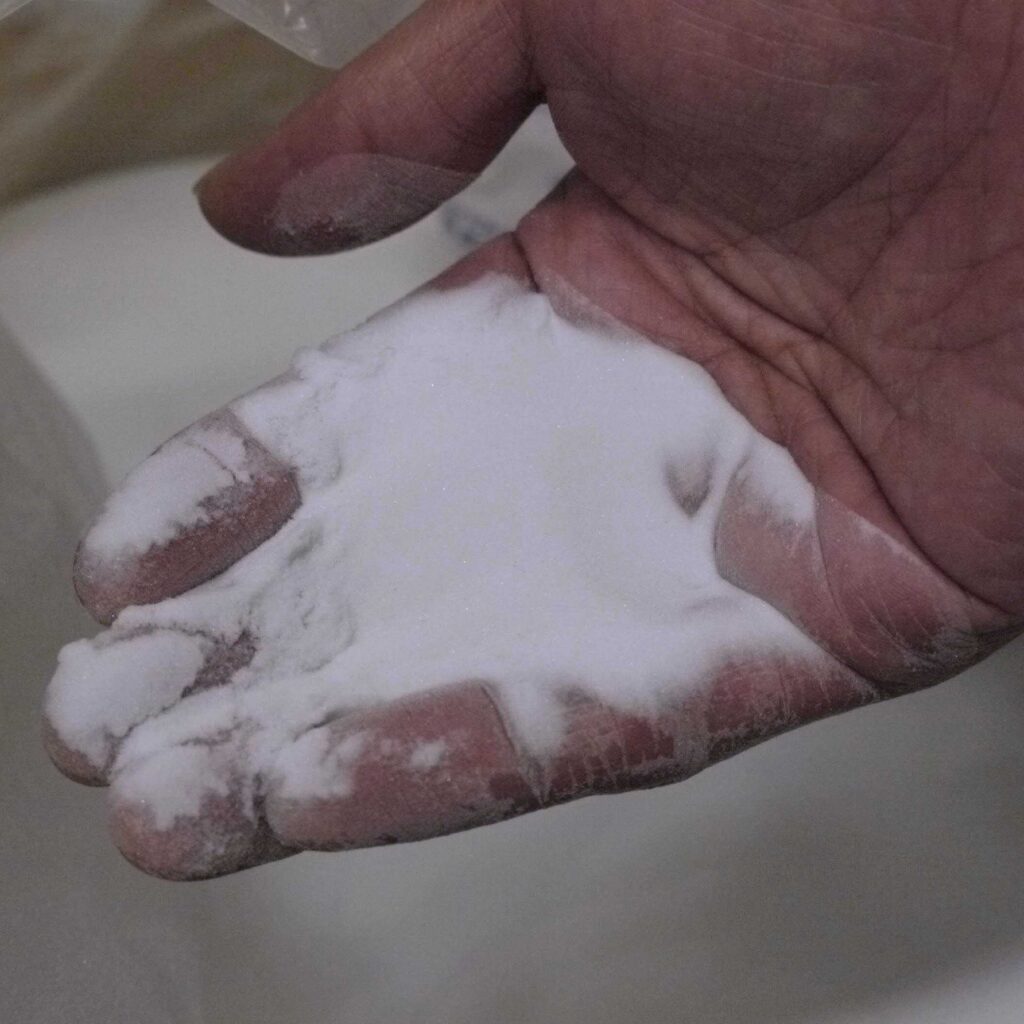
In contrast, parts with complicated shapes are sandblasted one by one by hand. An abrasive of suitable composition and size (for determining the grade of finish) are selected and the blaster gun located inside of a dust chamber is operated to give the metal parts the desired satin texture. The finished quality of the surface varies greatly depending on the distance between the target part and the blaster gun, the spray angle and spraying time. How homogenous the finish is depends entirely on the skill and experience of the operator.

Our sandblasted parts are plated before being assembled into products. To understand the true quality, hold a Cosina interchangeable lens in your hand and feel the metal parts. Even if anodized in black alumite or plated in chrome, the satin texture produced by sandblasting is recognizable.
We would like nothing more than for you to guess which parts were processed individually by hand one at a time.